The foundation of a terraced house was suffering from excessive moisture – here’s how the problem was fixed
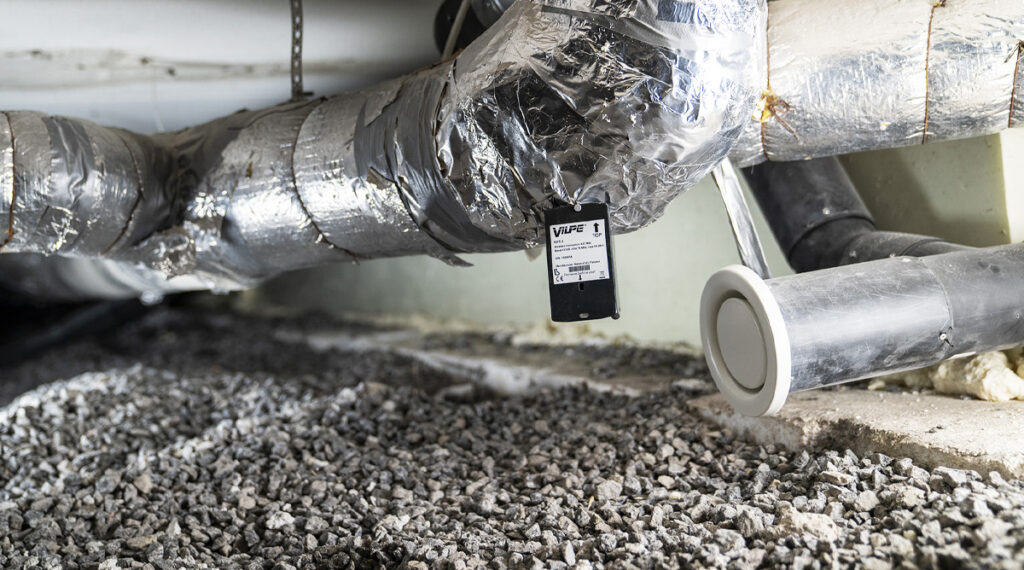
The chairman of a housing company in Korsholm, Finland, saw something worrying when he looked into the crawl space of a terraced house built in 2007: clear pieces of the load-bearing structure had been chipped away.
The chairman contacted the property manager, who contacted the engineering company Recon. The crawl space had been inspected before, but only now was it discovered that the problem was excessive moisture.
Load-bearing slabs made of Siporex lightweight concrete had been used in the crawl space. Siporex, made from steam-cured concrete, is more porous and lighter than ordinary concrete, so it insulates heat and sound effectively.
In the crawl space, however, the material has the disadvantage of reduced diffusion resistance due to its porosity. The water vapour in the air permeates the lightweight concrete effectively, and the high humidity in the crawl space thus causes significant moisture retention in the concrete. The elevated moisture content in the pores exposes the tensile reinforcement at the base of the concrete slab to corrosion.
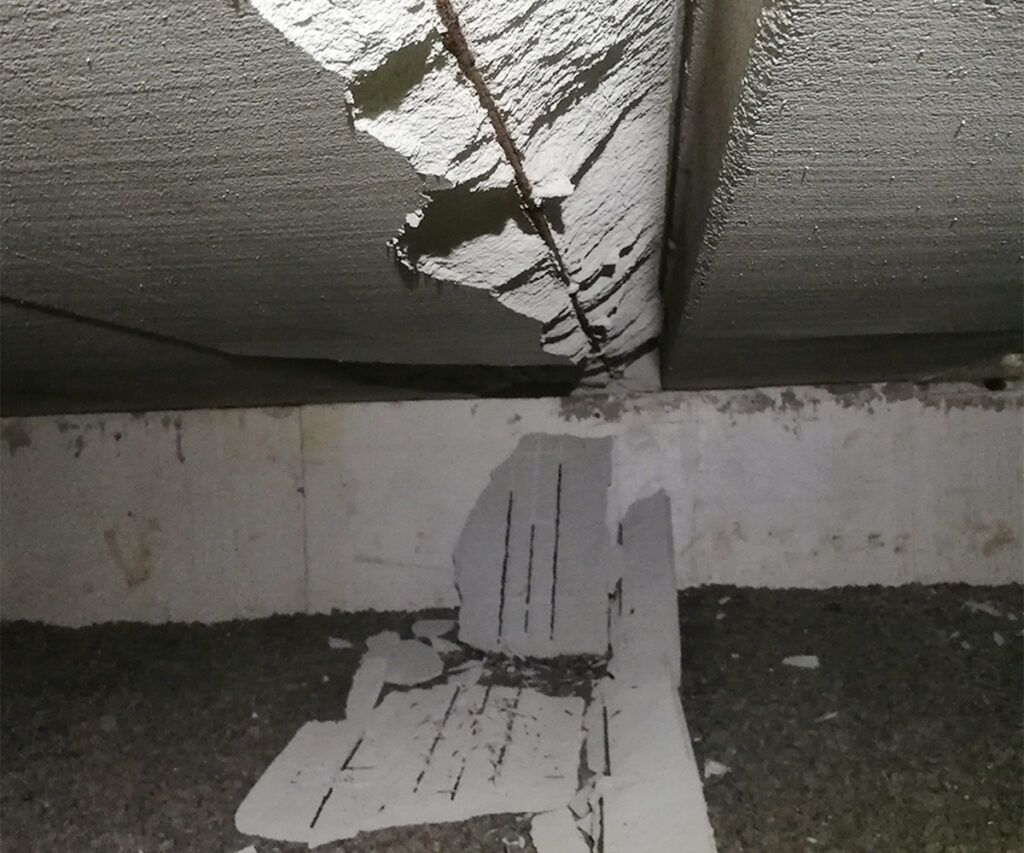
In addition, in one of the buildings, a pipe had leaked at some point in the past. A third cause of excessive humidity was that the roof fan ventilating the lower levels had stopped when its electrical connector came loose.
The housing company wished to continue using the roof fan to ventilate the lower levels of the buildings.
“I thought that a roof fan should have intelligent control. Sensors could measure the humidity outside and inside and calculate when it is advantageous to ventilate the crawl space. Was there really nothing like this on the market?” recalls Mika Iso-Oja from Recon.
Not just fixing the problem: fixing the root cause
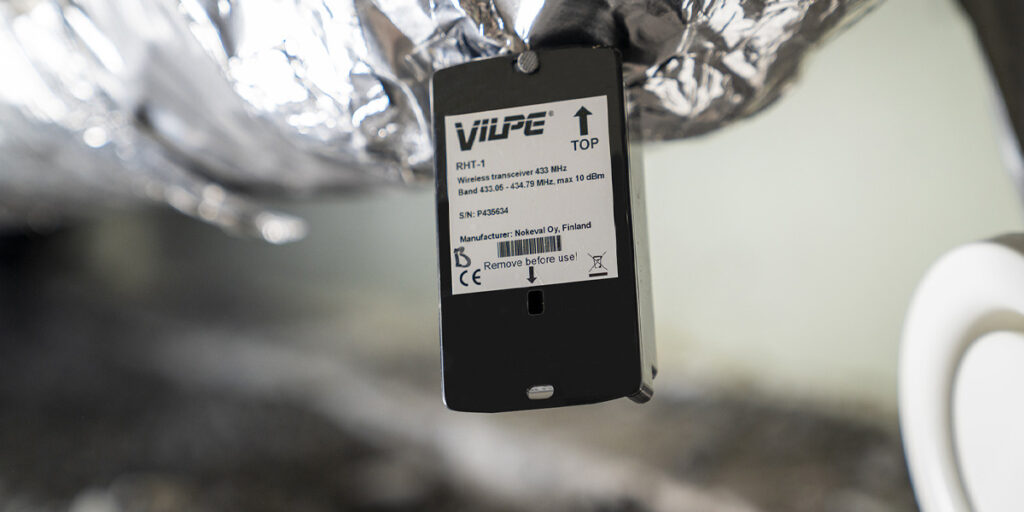
In making a plan for repairs, Iso-Oja wanted not only to fix the problem, but also to fix its root cause. The issue moved forward at the Toimivat katot (Working Roofs) building fair, where a colleague of Iso-Oja met a VILPE representative who explained the VILPE Sense system. At the same time, Iso-Oja was working on a plan of renovations for the site and heard about Sense from his colleague: the system was exactly what he needed.
“It was fascinating that I had thought of such a similar system, and then found it.”
The VILPE Sense system was installed in the lower levels of terraced houses B and C in October 2020, replacing the old roof fans with a VILPE Sense ECo roof fan.
The renovation also included the installation of collector channels in the buildings. This avoided the creation of stagnant areas that could impede ventilation.
How the crawl space was renovated
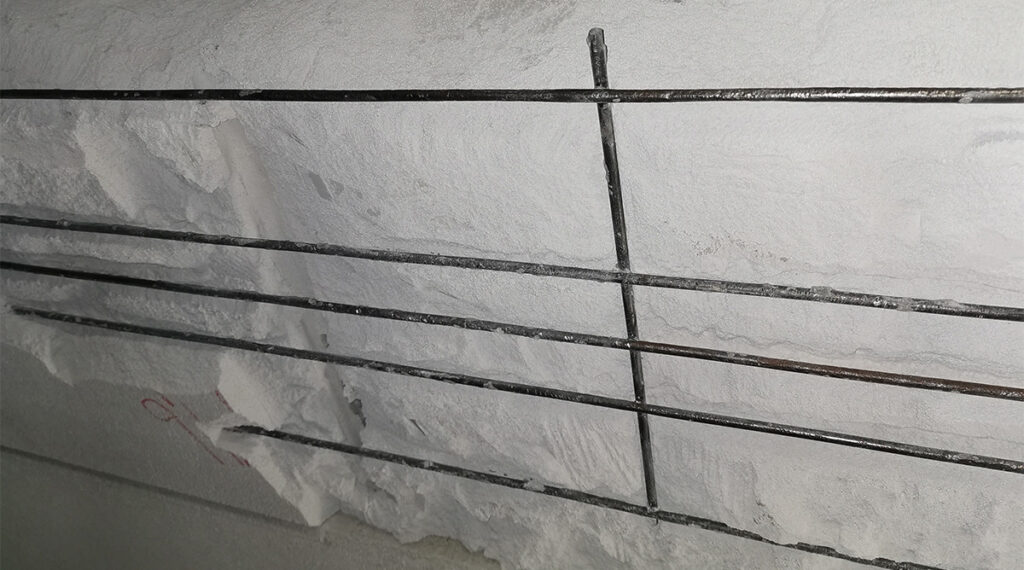
Demand-controlled ventilation with VILPE Sense ensures that problems do not recur. The underfloor slabs were renovated by cutting out the rusted rebar. The exposed reinforcement was cleaned of rust and protected with a cement-based product designed for the purpose.
A bonding surface was then created on the old lightweight concrete with adhesive mortar, after which the slabs were patched to the original level by filling the rough open area with cement-based mortar.
“Looking at the VILPE Sense data, you can see that conditions are now clearly better in the crawl space. The risk of damage to the steel is much lower,” says Iso-Oja.
If the moisture level rises in the crawl space, the VILPE Sense system reacts by increasing ventilation, which reduces the moisture load on the crawl space structures.
Help to detect problems early
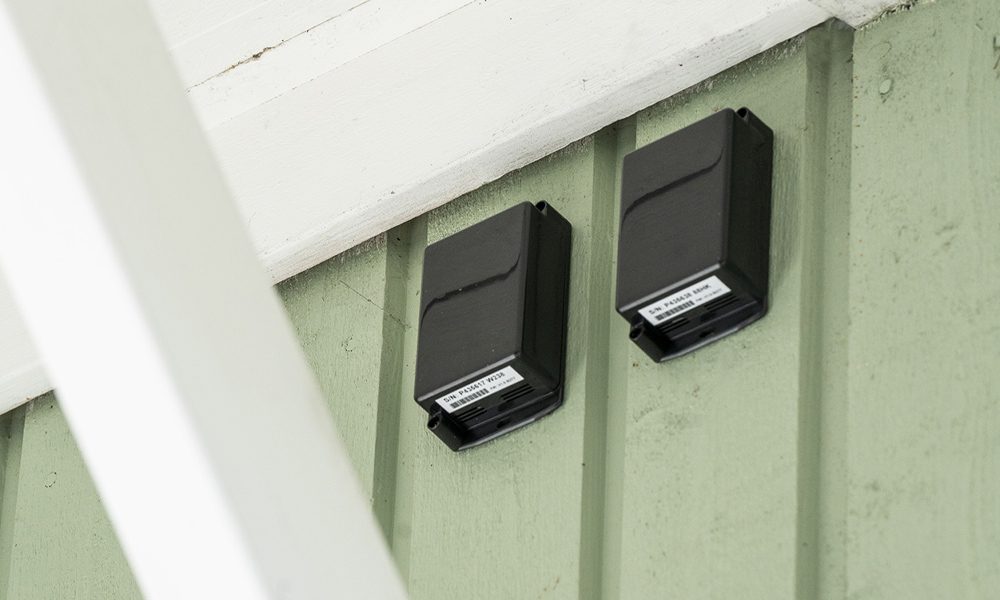
Automation makes it easier to monitor crawl space conditions.
“The intelligent control system is connected to the network. It has the advantage of knowing immediately if the system stops. If the problems in this building had been detected earlier, we would have got away with less damage,” says Iso-Oja.
The system has already reported a couple of outages.
“An alarm which draws attention to outages is a significant thing for any fan responsible for the mechanical extraction of a crawl space,” Iso-Oja says.
He studied the functionality of the system in his thesis as a civil engineer. Measurements showed that Sense was working properly. When viewed with a fog generator, air was moving evenly to all exhaust vents in the crawl space.
“Another advantage of Sense, based on my measurements, is that with the collector channels designed for the site, the air exchange is even and the typical problems of crawl spaces can be minimised.”
A smart system alerts you to problems
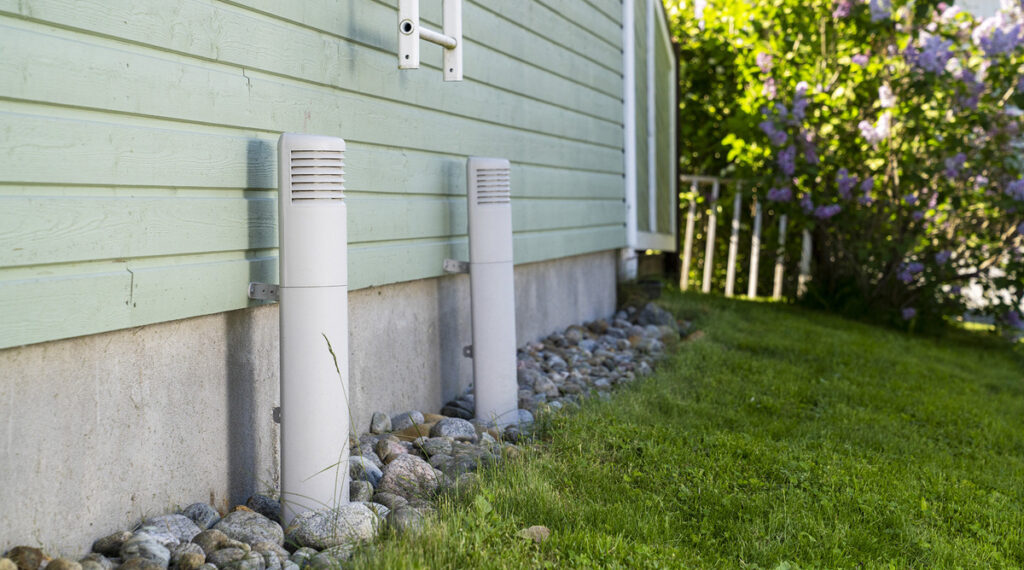
If the system alerts you that the humidity in the crawl space has risen to an abnormally high level, it is often worth checking. The problem could be a pipe leak, or malfunctioning drains when the snow melts in spring.
“There are many reasons, and that’s why I think it’s essential to use intelligent controls for crawl space ventilation that alert you to any problems. That way, they can be reacted to in good time, before they get worse.”
VILPE Sense can be used for the ventilation of roof structures in addition to crawl spaces. However, Iso-Oja feels that automatic ventilation is particularly useful under the floor, as moisture always tends to rise from the ground in the crawl space.
Read more about VILPE Sense.