Why Vapor Barriers Matter
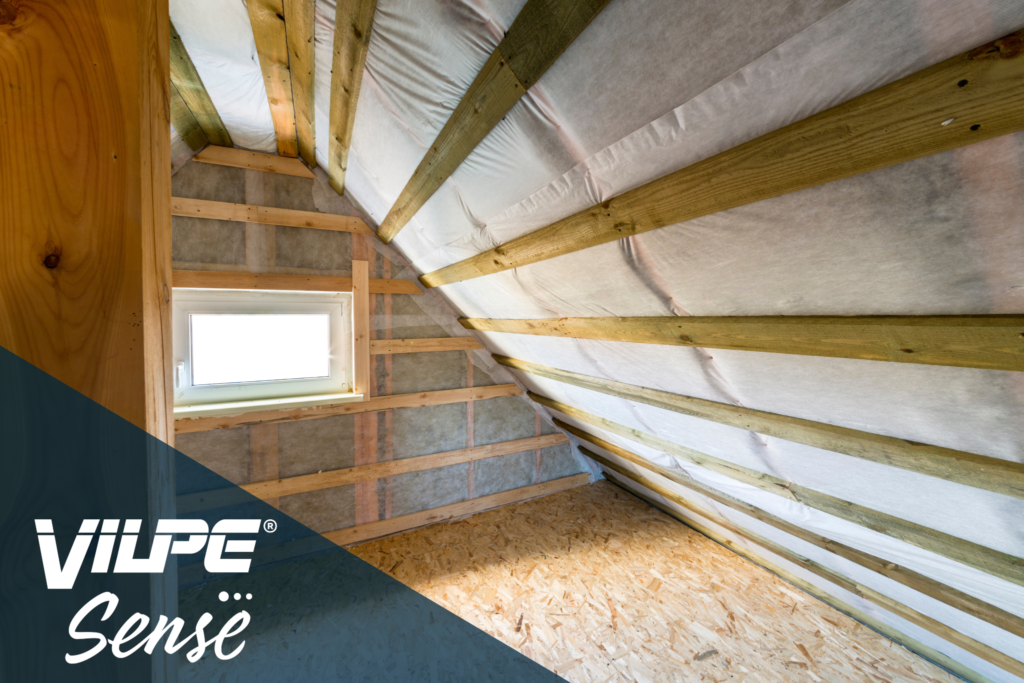
Moisture infiltration is a significant concern for both pitched and flat roofs (Gullbrekken, Rüther and Kvande, 2017). Common moisture sources include condensation, air leakages, and precipitation. While precipitation is the most common culprit, condensation—driven by temperature differences between indoor and outdoor environments—can be equally damaging. When warm, humid air encounters cooler surfaces within the roof, it condenses into liquid water. Over time, this buildup compromises insulation, promotes mold growth, and can lead to structural damage.
Moisture build-up in flat roofs
Warm air carries moisture as vapor. When it passes through permeable materials in the roof and meets cooler surfaces, it condenses into water. Significant temperature contrasts—such as in cold climates during winter or in air-conditioned buildings in warm regions—intensify the risk of condensation (Gullbrekken, Rüther and Kvande, 2017). Poor insulation or inadequate sealing exacerbates these issues, leading to mold growth, reduced insulation efficiency, and potential structural damage.
What are vapor barriers and what do they do?
A vapor barrier is a low-permeability layer designed to prevent water vapor from traveling through a roof assembly (Bunkholt et al., 2020). By blocking moisture-laden air from cooler roof surfaces, it helps preserve the integrity of the structure and maintains indoor air quality. Common vapor barrier materials include polyethylene sheeting and bituminous membranes.
- Cold climates: Typically installed on the warm (interior) side of the insulation to keep indoor moisture from reaching colder roof layers.
- Warm or humid climates: Placed on the exterior side of the insulation (especially in air-conditioned buildings) to block humid outdoor air from condensing on cooler interior surfaces.
By preventing moisture infiltration, vapor barriers help maintain insulation performance, reduce energy consumption, and extend the lifespan of both insulation and roofing materials.
Challenges and risks of vapor barriers
Although essential in many roof assemblies, vapor barriers come with potential pitfalls or challenges:
- Moisture trapping: An incorrectly placed or poorly installed barrier can trap moisture within the roof, worsening condensation problems.
- Reduced drying potential: The same layer that prevents vapor entry also restricts moisture escape, prolonging wet conditions.
- Compatibility issues: Some roofing materials may not perform well with certain vapor barriers, leading to chemical or functional incompatibilities.
Proper placement, careful installation, and thorough sealing are critical. Even minor gaps, tears, or misalignments can undermine a vapor barrier’s effectiveness.
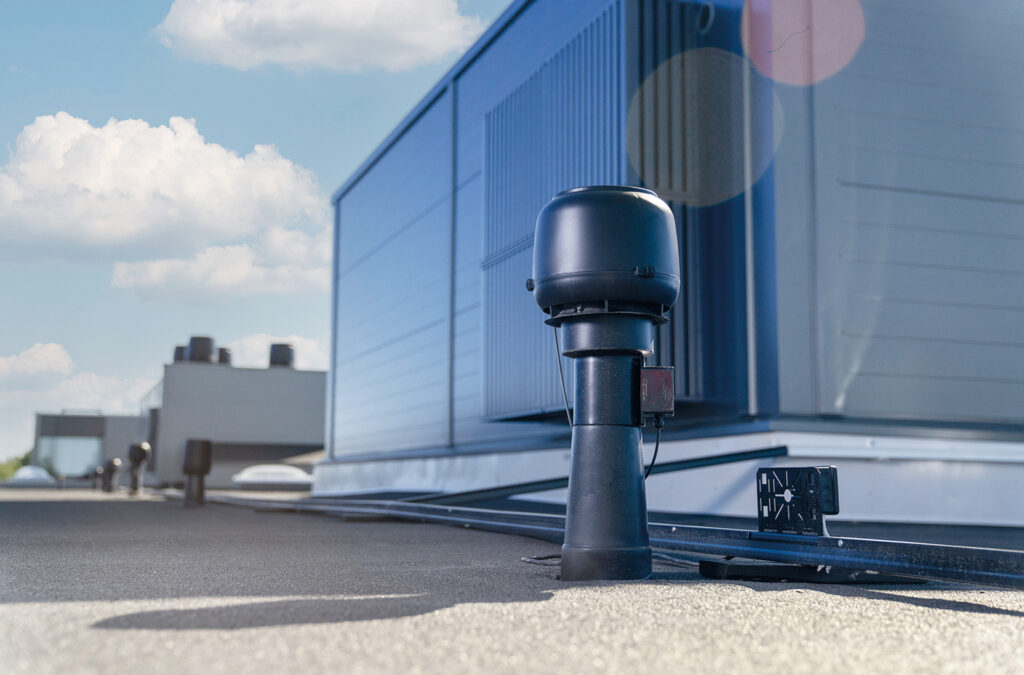
Complementary strategies with demand-based ventilation
Ventilation of roof structures is a long-standing method for moisture management. Traditionally, this involves creating airflow within the roof assembly, allowing structures to dry over time. However, conventional approaches cannot precisely control the timing or intensity of ventilation. This can lead to situations where ventilation occurs even when incoming air is humid or when the roof structures do not require drying.
Modern demand-based systems address this issue by continuously monitoring conditions and adjusting ventilation rates accordingly. One example is VILPE Sense humidity control, which measures humidity levels in real time and alerts building owners when those levels increase. By controlling roof fan operation, it helps ensure that ventilation is provided only when needed and in optimal conditions. In this way, structures are not ventilated unnecessarily in humid weather or when they are already dry, reducing the risk of condensation and improving overall energy efficiency.
In addition to ventilation controls, proper insulation significantly influences roof performance. Materials should be chosen with the appropriate R-values for the region and installed without gaps or voids, ensuring that warm, moisture-laden air does not readily encounter cooler surfaces where condensation might form. Air sealing completes this protective framework by minimizing air leaks around penetrations and transitions, further reducing the movement of moist air into vulnerable areas.
Routine maintenance and monitoring
Regular inspections are vital for identifying minor issues before they escalate. Simple checks for leaks, damaged flashing, or compromised seals can prevent larger problems. Integrating humidity sensors into the roof system offers timely data on moisture levels and enables proactive adjustments. Taken together, careful attention to demand-based ventilation, high-quality insulation, thorough air sealing, and ongoing maintenance creates an integrated strategy that mitigates condensation risks and promotes a durable, energy-efficient roof assembly.
References:
Bunkholt, N. S., Gullbrekken, L., & Kvande, T. (2020). Influence of local weather conditions on ventilation of a pitched wooden roof.
Gullbrekken, L., Rüther, P., & Kvande, T. (2017). Air leakage of defects in the vapour barrier of compact roofs.